Mastering MIG welding with adjustments, equipment and techniques
Discover essential adjustments, equipment tips, and expert techniques to accelerate your MIG welding game by reading our article in the October issue of The Welder. You’ll learn how to balance voltage and wire feed speed for flawless welds, select the right welder and shielding gas, and master gun angle and travel speed. Plus, we’ll guide you through troubleshooting common challenges to ensure consistent, high-quality results. Don’t miss out on transforming your welding skills—dive into the full article now!
Introducing The Bernard® Clean Air E™
Introducing The Bernard® Clean Air E™
Welding professionals face daily challenges in keeping their work environment clean and safe. With strict weld fume regulations, effective fume control is more important than ever. The Bernard® Clean Air E™ fume extraction MIG gun helps by capturing welding fumes directly at the source without sacrificing performance.
Why Source Capture Matters
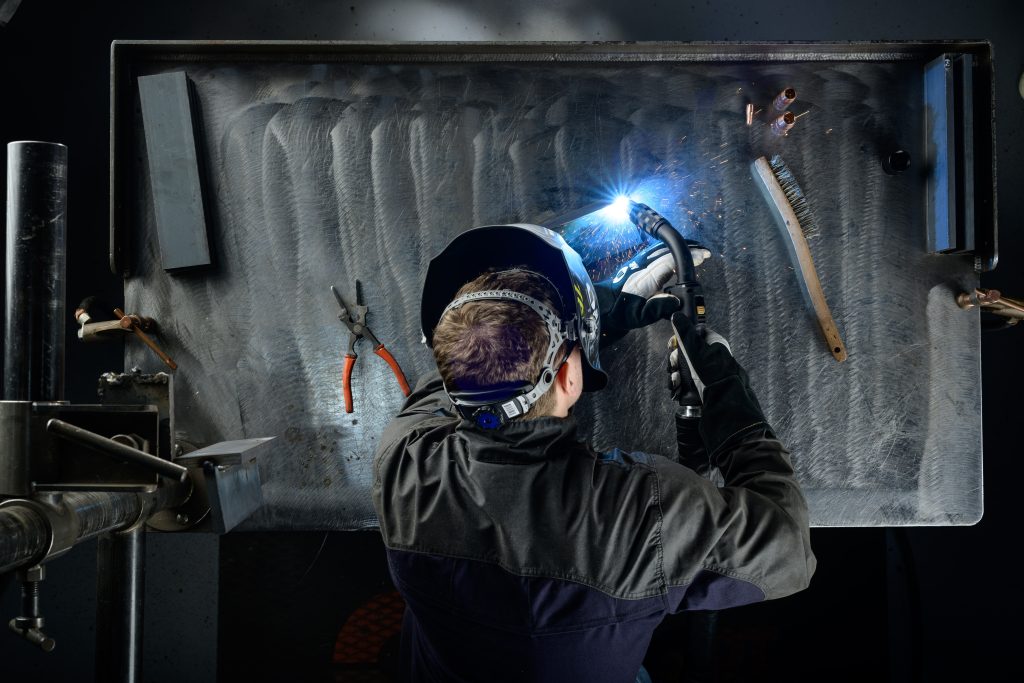
Capturing weld fume as close to the point of generation as possible, also known as source capture, is one of the most effective ways to reduce exposure. Unlike general ventilation or ambient air systems that dilute fumes, source capture methods like fume extraction guns immediately remove hazardous particles, helping improve air quality for operators and surrounding workers.
The Clean Air E™ captures up to 95% of fume at the source. The gun is built with adjustable extraction control through interchangeable shroud lengths and a slider allowing operators to fine-tune suction levels without affecting shielding gas coverage. This balance is critical for maintaining weld quality while maximizing fume capture.
Key Benefits of the Clean Air E™
Efficient Extraction
By removing up to 95% of fumes directly at the arc, the Clean Air E™ helps reduce exposure risks and contributes to a cleaner workspace.
Enhanced Ergonomics
With a lightweight handle design, the Clean Air E™ allows you to weld longer without fatigue. The ball swivel at the rear of the handle makes maneuvering easier, even in difficult positions.
Engineered for Endurance
This fume gun is built to withstand the toughest working environments. Made from durable, tested materials, it features a robust and straightforward design for easy maintenance.
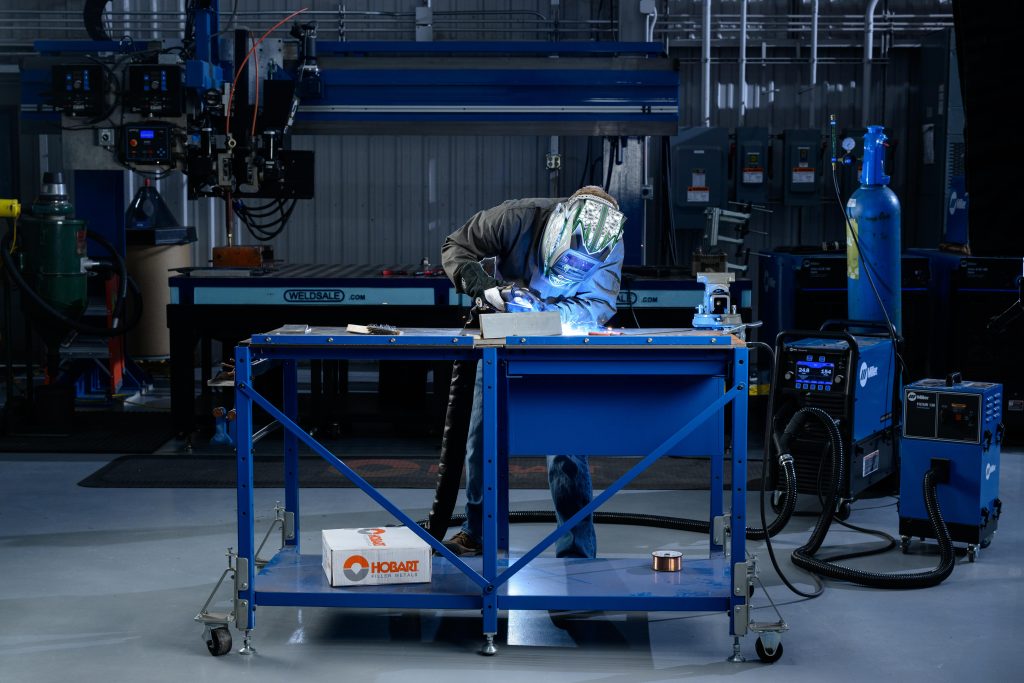
Designed for Demanding Applications
Ideal for high-amperage and high-deposition rate applications, the Clean Air E™ is well-suited for industries such as: Shipbuilding, Heavy equipment manufacturing, General fabrication and manufacturing
Ergonomic and Easy to Use
Unlike bulky ventilation systems, fume extraction guns like the Clean Air E™ seamlessly integrate into a welder’s workflow. With a lightweight, ergonomic design and a user-friendly adjustment slider on the guns handle, it operates much like a standard MIG gun while providing the added benefit of fume extraction.

Customizable
We know every welder has their own preference when it comes to welding style. That’s why we designed two trigger options—a button and a lever, plus an extended lever for added comfort. We also made the shrouds interchangeable, offering three lengths to optimize either weld visibility or fume extraction, depending on your application.
A Smarter Step Toward Safer Welding
No single solution eliminates all welding fume exposure, but using a fume extraction gun alongside a compatible extraction unit like the Miller® Filtair®215 can significantly improve a workplace environment. The Bernard® Clean Air E™ provides a practical, effective way to prioritize welder safety and performance.

It starts at the source™
Effective June 20th, 2025, the following Elliptical series diffusers will be discontinued from our product offering: These diffusers allowed Elliptical series consumables to be compatible with Tweco® and Tregaskiss® style MIG guns. While there are no direct replacements for these parts, we suggest converting to AccuLock™ S consumables. For Tweco® style MIG guns, AccuLock™ S consumables can be installed by using adaptor 1380030. No adaptor is needed for Tregaskiss® MIG guns. For an easy change-over, we offer AccuLock™ S conversion kits complete with a variety of tips, nozzles, diffusers and Tweco® adaptor. Kit Part Number: ALCSK-1 If you have any questions, please contact Customer Service by phone 855.MIGWLED (644.9353) or by email cs@itwmig.com. Effective April 22, 2025, we have simplified our BTB MIG Gun configurator selections. Check out your Best of The Best MIG Gun options below: BTB MIG Gun configurations that include options not listed above will still remain available for purchase. Our Reverse Lookup tool can help provide a parts breakdown for ordering information. If you have any questions or would like more information, please contact Customer Service by phone at 1.855.MIGWELD (644.9353) or email at cs@itwmig.com. Welders must be able to rely on every aspect of their equipment, and consumables are an integral component of a high-quality weld. When you notice an uptick in downtime and consumables consumption, it’s time to take a deeper look at what the culprit could be. An easy place to start is by looking at the quality of the consumables you’re using. Lower-quality consumables can lead to major expenses in the long run — as seen in lost production, weld rework and the cost of constant replacements. Original equipment manufacturer (OEM) consumables are the right choice for improved operations and consistent, high-quality welds. Below are four reasons you should consider investing in genuine consumables over lower-quality options. Even the best MIG guns or the most highly trained operators cannot offset the impact of poorly made consumables on performance. OEM consumables are manufactured using high-quality materials, which helps deliver the arc stability needed to create smooth, even welds with minimal defects. In addition to helping improve weld integrity and facilitating more durable weld joints, genuine consumables also help prevent excessive spatter and minimize post-weld cleanup. Because OEM consumables are manufactured for reliability, they have consistent diameters and surface conditions that ensure smoother feeding through the gun. By contrast, non-genuine consumables are often made from low-quality materials and may not consistently meet key manufacturing specifications. 2. OEM consumables are expertly designed to be reliable Genuine consumables are backed by research, technology and expertise, having been produced to ensure the material composition and mechanical properties are consistent and reliable. Keeping those details at the forefront makes for stable arcs, high-quality welds, fewer points of failure and simplified maintenance. Their ease of use can even help to reduce welder training times and shorten your troubleshooting list if problems do arise. Copycat manufacturers are also less likely to submit their consumables to the rigorous testing and quality assurance processes that OEMs follow. AccuLock ™ consumables have been designed to flawlessly integrate into Bernard® semi-automatic and Tregaskiss® fixed automatic and robotic MIG welding guns and to address welders’ most common pain points. For semi-automatic MIG welding applications, the AccuLock™ S consumables system paired with front load E-Z Feed™ liners reduces liner trim length errors and erratic wire feeding while simultaneously increasing contact tip life. The front load liners are locked and concentrically aligned to both the contact tip and power pin. This eliminates misalignment and provides a flawless wire feed path, ensuring uninterrupted delivery of the wire to the weld puddle. As a result, operators have fewer burnbacks, bird nests and erratic arcs. The AccuLock R consumables system is available for robotic or fixed automatic MIG welding applications. With these consumables, operators have the opportunity to realize significant improvements, like increasing contact tip life span and decreasing issues with contact tip cross-threading. For operations constantly managing complex or costly consumables inventories, AccuLock S and AccuLock R consumables systems share a common contact tip — making for simplified part inventory across mixed fleets of semi-automatic and automated welding applications. Operations who are looking to get more life out of their consumables but aren’t using Bernard or Tregaskiss guns can purchase the conversion series consumables to still experience the benefits of a high-quality system. A good OEM is invested not only in the performance of its products but also in the overall user experience, which extends to customer service. Reputable OEMs usually have expert technical support teams that help with troubleshooting and provide solutions if something goes wrong. They can also share product tips and offer advice, like how to make your MIG gun consumables last longer. However, if you’re using nongenuine consumables and parts, technical support teams are unable to offer such assistance. Often, if an issue arises involving lower-quality parts, it will be essential to order genuine parts and wait for them to arrive to see if the issue still occurs before the OEM team can offer support. Using genuine parts from the get-go means you can get expert advice right away — or avoid issues altogether. 4. OEM products can have a longer life Because OEMs are making greater investments in materials, design and testing, that means OEM consumables usually cost more than low-quality consumables. But, as the saying goes, you get what you pay for. Consumables are probably not your biggest cost — labor is. So any money you save by using cheaply made consumables could be offset by the extra labor required to frequently change tips, troubleshoot equipment failure or rework a faulty weld. Those looking for superior performance and longevity find that OEM options can equate to more arc-on time — and more products out the door. AccuLock contact tips are designed so that 60% of the tip is buried within the diffuser for less exposure to the heat of the arc and more cooling from shielding gas. This gives the tip a life that can be two to three times longer than other tips. All told, because genuine consumables are designed specifically for your MIG welding gun, they can last longer, be more reliable and deliver higher-quality welds — ultimately enhancing the operator experience and your welding operation’s bottom line. For Immediate Release BEECHER, Ill./WINDSOR, Ontario (March 20, 2025) — Bernard announced the release of the new Clean Air E™ fume extraction MIG gun, the newest high-efficiency fume extraction gun in the brand’s lineup. Crafted for efficient extraction, enhanced ergonomics and engineered endurance, this gun sets a new standard in MIG welding fume capture technology. With an ongoing priority to ensure safer, cleaner work environments for operators coupled with heightened fume standards being implemented across the country, Bernard saw an opportunity to evolve the standard fume extraction gun to maximize its efficiency and usability. Bernard took customer and welder feedback and designed a product that would be the most impactful for welders in a next-generation fume extraction gun. The team applied that feedback throughout the research and development process until it resulted in the Clean Air E™, which offers solutions to common operator pain points, including: · Efficient extraction: The Clean Air E™ achieves up to 95% fume capture right at the source, which improves air quality in the workspace and reduces OSHA-related risks. · Enhanced ergonomics: The ergonomic design reduces strain and fatigue on welders, which allows them to focus on precision and quality for extended use. · Engineered for endurance: The Clean Air E™ features durable components and long-life consumables, which reduces downtime and maintenance costs, delivering a lower cost of total ownership. “When it comes to welding, operators seek the trifecta in their gun: ergonomics, extraction performance and ease of maintenance,” said Jerome Parker, product manager, Bernard. “The Clean Air E™ was designed alongside actual users to ensure we arrived at a solution that redefined traditional fume capture guns for the modern welder, enhancing both their operator experience and their weld environment.” On the gun itself, the Clean Air E™ offers enhanced features for easier and more efficient use: · Improved weld access: Three nozzle shroud lengths allow operators to balance fume capture with weld access and improved visibility of the weldment. · Instant flow adjustment: The new flow control slide on the back of the handle enables welders to easily reduce airflow by up to 10 cfm to help overcome porosity issues. · Upgraded handle comfort: Two handle styles are available to suit different grip styles and hand sizes, with internals contoured to enhance airflow and fume capture. The lever trigger can also be mounted on top for additional comfort. · Increased flexibility: A durable, lightweight aluminum ball swivel at the end of the handle provides 15 degrees of extra flex in any direction for additional improved ergonomics. · Maximized airflow: A new Y-connector offers contoured internals that maximize airflow, with a vacuum outlet that is compatible with any fume extraction unit. For a premium fume extraction pairing, operators have the option to connect the Clean Air E™ to the Miller® FILTAIR® 215. Learn more about how the Clean Air E™ can deliver safety, performance and comfort for welders at https://www.startsatthesource.com/ About Bernard Bernard, a leading manufacturer of premium semi-automatic MIG welding guns and consumables, is dedicated to enhancing welding productivity and performance. Headquartered in Beecher, Illinois, Bernard is known for innovative solutions that prioritize operator comfort, ease of maintenance, and exceptional durability. Bernard is a proud brand of Illinois Tool Works Inc. (NYSE: ITW). For more information, visit BernardTregaskiss.com, call 1-855-MIGWELD (1-855-644-9353), email CS@itwmig.com. Contact: Lauren Smith, Hiebing for Bernard/Tregaskiss phone: +1 6082684408 lsmith@hiebing.com Keep your Bernard® Clean Air E™ Fume Extraction MIG Gun performing at its best by replacing the Y-connector when needed. This quick guide walks you through the simple steps to ensure a secure fit and maintain optimal fume extraction efficiency. Watch now to keep your system running smoothly and your workspace cleaner. Instructions Separate connector halves. Push rear hose swivel forward to slide it out of the cavity. Slide the hose assembly forward and remove the remaining Y Connector half. Place the new rubber boot into the new Y Connector set. Position the cable assembly in the Y Connector channel, ensuring proper alignment with rubber boot. Pull the hose assembly back into the swivel cavity and ensure it is taut (no slack). Confirm the hose and cable assemblies are properly seated and secure. Align the Y Connector halves and reinstall screws. Find more resources at www.startsatthesource.com Properly connecting your Bernard® Clean Air E™ Fume Extraction MIG Gun to a fume extraction unit is key to maximizing performance and maintaining a cleaner work environment. In this video, we walk you through the simple steps to ensure a secure and efficient connection, helping you get the most out of your fume extraction system. Instructions Thread hose onto the fume port of the fume extraction unit and tighten securely. Attach the opposite end of hose to the 1-3/4” port on the Y Connector, ensuring all connections are tight. Find more resources at www.startsatthesource.com Maintaining your Bernard® Clean Air E™ Fume Extraction MIG Gun is quick and easy! Watch as we walk through the simple process of replacing the neck and trigger, ensuring your gun stays in top working condition. Designed for durability and performance, the Clean Air E™ makes maintenance hassle-free so you can focus on the job. Instructions Changing the Inner Neck Assembly Remove the Shroud and Consumables: Unthread the knurled smoke shroud from the smoke tube assembly and remove the front end consumables. Separate the Handle Halves: Remove the socket head cap screws (7/64″ hex) and keep them for later. Remove the Smoke Tube Assembly: Slide it forward and off the inner neck assembly. Loosen the Lock Nut: Place the neck in a vise (don’t over-tighten). Use 3/4” wrenches to loosen the lock nut on the neck. Unthread the Neck: Once the lock nut is loose, unthread the neck from the end fitting by hand. Replace the Neck: Add the lock nut to the new neck, thread it into the cable end fitting, and tighten by hand. Secure the neck in a vise and torque the lock nut/end fitting connection to 30 ft-lbs (40.7 Nm). Reassemble the Handle: Position the neck and smoke tube assembly into the handle. Ensure the trigger components and vacuum slide are correctly placed, with trigger wires routed properly. Secure the Handle Halves: Use the handle screws and torque them to 10 in-lbs (1.1 Nm). Changing the Switch – Button Model Separate the Handle Halves: Remove the screws completely. Remove the Terminals: Use needle nose pliers to remove the terminals from the trigger switch. Attach the New Trigger: Secure the terminals to the new trigger, position it in the right handle half, and ensure the wires are routed correctly. Reassemble the Handle: Reinstall the second handle half, tighten all screws, and torque to 10 in-lbs (1.1 Nm). Changing the Switch – Lever Model Separate the Handle Halves: Remove the screws completely. Remove the Switch Assembly: Use needle nose pliers to disconnect the terminals and carefully remove the lever. Attach the New Switch: Secure the terminals to the new switch assembly, install it into the mounting cavity, and reinstall the lever. Reassemble the Handle: Ensure all components are correctly positioned, then reinstall the second handle half, starting with the lever screw. Tighten all screws and torque to 10 in-lbs (1.1 Nm). Changing the Vacuum Slide Switch Separate the Handle Halves: Remove the screws completely. Remove the Slide Switch: Carefully take it out of the channel in the handle half. Install the New Slide Switch: Position it in the channel, ensuring it moves freely. Reassemble the Handle: Keep the slide switch properly aligned and reinstall the screws, tightening them evenly and torquing to 10 in-lbs (1.1 Nm) Find more resources at www.startsatthesource.com We designed the Bernard® Clean Air E™ Fume Extraction Gun with interchangeable shrouds, giving you the flexibility to optimize fume capture for your specific welding application. Choose from a longer shroud for maximum fume extraction, a medium shroud for the perfect balance of weld access and fume capture, or a short shroud for maximum weld access while still extracting fumes. Instructions Simply unthread the fume shroud from the neck tube and rethread your desired shroud based on your nozzle size and welding application. Find more resources at www.startsatthesource.com Need to replace the hose on your Clean Air E™ fume extraction gun? We’ve got you covered! Follow these simple steps to swap it out quickly and keep your fume extraction system performing at its best. Watch now and ensure clean, efficient welding every time. Instructions 1. If replacing the vacuum hose assembly, remove all screws to separate the handle halves and remove the front hose swivel from its cavity. 2. Remove screw covers and two screws securing the rear handle, then slide the rear handle and strain relief backward to remove them. 3. Remove screws on the Y Connector and open to expose the cable assembly and rear hose swivel. 4. Pull the vacuum hose assembly backward to remove it from the cable assembly. 5. Slide the new vacuum hose assembly forward over the cable assembly until the front hose swivel rests in its cavity. Align the handle halves and reinstall all screws to retain hose assembly within handle. 6. With the cable straight, pull the hose and position it into the Y Connector, ensuring no slack. Tighten Y Connector screws, correctly positioning rubber boot within the Y Connector. 7. Slide rear handle and strain relief forward onto the cable assembly and secure with screws and screw covers. Find more resources at www.startsatthesource.com The Occupational Safety and Health Administration (OSHA) and other safety regulatory bodies set the allowable exposure limits for weld fumes and other particulates, including hexavalent chromium, with the aim of protecting employees against potential health hazards in the workplace. Providing welding operators with proper ventilation during the welding process is an important step companies can take to help meet the standards — and to help provide a safe and comfortable work environment. Companies may opt to invest in centralized fume extraction systems, which are designed to protect the entire shop area. These systems involve the installation of new ductwork and fans to remove fumes and are highly effective, but they are also more expensive than other options. A viable alternative for some companies is a fume extraction gun used in conjunction with a fume extraction device or localized filtration system. Fume extraction guns are available in a variety of amperages (typically 300 to 600), cable styles and handle designs. As with any welding equipment, they have their best applications, advantages and limitations, as well as recommended techniques for achieving the best results. Fume extraction guns operate by capturing the fume generated by the welding process right at the source, over and around the weld pool. The weld fumes removed by these guns are composed of a combination of the filler metal and base material. Various manufacturers have proprietary means of constructing guns to conduct this action, but at a basic level they all operate similarly: by mass flow, or the movement of material. A vacuum chamber suctions the fumes through the handle of the gun, into the gun’s hose and through to a port on the filtration system (sometimes informally referred to as a vacuum box). Typically, fume extraction guns are larger than regular welding guns, and include the vacuum and hose that are necessary to extract the fumes. Some manufacturers offer fume extraction guns with a vacuum hose swivel on the rear of the handle to make them easier to maneuver. Also, design advancements have minimized the handle weight and size to make the guns as light as possible for operator comfort, while still offering consistent fume extraction benefits. The Bernard® Clean Air E™ fume extraction gun is designed to efficiently capture welding fumes at the source, helping to create a cleaner work environment. This gun is particularly well-suited for applications using solid welding wire and for operations in confined spaces, where fume extraction directly in the welding operator’s breathing zone is essential. Industries that frequently benefit from this technology include shipbuilding, heavy equipment manufacturing, and general fabrication, especially when working with mild or carbon steel. Additionally, for applications in petrochemical industries or those involving stainless steel welding, where higher levels of hexavalent chromium are present, the Clean Air E™ gun provides an effective solution for improving air quality. Designed for high-amperage and high-deposition rate applications, this gun performs best in flat and horizontal welding positions, where it can effectively capture rising fume particles. While fume extraction in out-of-position welding can be more challenging due to the natural rise of fumes, proper technique and positioning can help maximize effectiveness. The Clean Air E™ fume extraction gun operates similarly to a standard MIG gun, making it easy for welding operators to adapt to. To achieve the best results, consider these best practices: By integrating the Bernard® Clean Air™ E fume extraction gun into your welding operations, you can enhance fume control while maintaining welding quality and efficiency. Fume extraction guns operate by capturing the fume generated by the welding process right at the source, over and around the weld pool. As with any piece of welding equipment, fume extraction guns benefit from preventive maintenance. Flux-cored wire allows vacuum adjustment Because flux-cored wire produces a slag, it generates more weld fume. However, one benefit of using self-shielded flux-cored wire, for example, is it allows the ability to increase the vacuum level of the gun. Welding operators can close off all the vents and utilize the long shroud. This action maximizes the vacuum at the front end of the gun without concern for disturbing the shielding gas, since there is none generates with self-shielded flux-cored wire. When using gas-shielded flux-cored wire, a 0 to 15-degree angle will help maximize fume collection. Pause at the end At the end of the weld, welding operators can pause for 10 to 15 seconds, holding the fume extraction gun in place without depositing weld metal. This action allows the gun to capture residual fumes as the weld bead is cooling. Wire type determines stickout The contact tip to work distance can be longer — about 1/2 inch to 3/4 inch — when welding with flux-cored wire and a fume extraction gun. With solid wire, welding operators should try to keep the stickout to 1/2 inch or less to maximize fume capture. These lengths are comparable to the stickout lengths used with standard MIG guns. Experiment with the air control regulator Some guns, like the Clean Air E™, incorporate a slider or toggle mechanism conveniently located on the gun handle, while others integrate this function internally. This adjustability is essential for balancing fume extraction with shielding gas coverage. Too much suction can disrupt the protective gas flow, leading to weld defects like porosity, while too little may not effectively capture harmful fumes. By using the built-in adjustment feature, operators can increase or decrease suction as needed to maintain optimal fume control while ensuring proper weld protection. Finding the right balance may require some trial and error. To optimize performance, welding operators should test the air control setting on scrap material before welding on a final product. This ensures that fume extraction is maximized without negatively affecting weld quality. With the Clean Air E™ and other adjustable fume extraction guns, operators have greater control over their work environment—helping to improve air quality while maintaining welding efficiency. As with any piece of welding equipment, fume extraction guns benefit from preventive maintenance. Caring for them is similar to caring for a standard MIG gun. Also note that using flux-cored wire with these guns requires more frequent gun maintenance than solid wire because of the slag and fumes it generates. Regular maintenance is important to help prevent a clog or spatter buildup, which can limit the fume capture rate. Inspecting and maintaining the front end of the gun is key to optimizing fume extraction. Frequently inspect the nozzle and contact tip for signs of spatter buildup, which along with blocking the fume extraction can also obstruct shielding gas flow and cause weld defects. Spatter buildup also can cause consumables to fail prematurely. Replace the consumables if spatter buildup appears, or clean them according to the manufacturer’s recommendations. Also, inspect the vacuum hose regularly for damage such as cuts or kinks, which can lead to loss of suction. Replace a damaged vacuum hose as necessary. Regarding consumables, using the manufacturer’s recommended consumables package with a fume extraction gun helps optimize performance, as the guns are engineered to get the best results with specific consumables. When in doubt about maintenance or any other aspect of using a fume extraction gun, consider working with a trusted welding distributor, certified industrial hygienist and/or the gun manufacturer to address any questions or concerns. In combination with many other variables in the welding operation — wire selection, specific transfer methods and welding processes, welding operator technique, and base material selection — fume extraction guns can help companies maintain compliance with safety regulations and create a cleaner, more comfortable welding environment. Proper use and maintenance of the equipment is important to get optimal results.
New industry standards from the Occupational Safety and Health Administration (OSHA) are protecting employees against potential health hazards in the workplace. These regulations, which dictate allowable exposure limits of welding fumes and other particulates (including hexavalent chromium), have led many companies to invest in fume extraction equipment. An increased desire to maintain optimal welding operator safety and to attract new skilled welding operators to the field is also a consideration in investing in this equipment — companies want to create the most comfortable and healthy work environment possible. The Clean Air E™ MIG fume extraction gun, as shown here, operates by capturing the fume generated by the welding process right at the source, over and around the weld pool. With interchangeable shroud options to help customize your extraction for your application. Some companies may opt for centralized fume extraction systems, which are designed to protect the entire shop area. These systems involve the installation of new ductwork and can be a costly investment for capturing fume particulate in the air. Fume extraction guns are available in a variety of amperages, cable styles and handle designs. As with any welding equipment, they have their advantages and limitations, best applications, maintenance requirements and more. In combination with many other variables in the welding operation; welding wire selection, specific transfer methods and welding processes, welding operator behavior and base material selection — fume extraction guns can help companies maintain compliance with safety regulations and create a cleaner, more comfortable welding environment. Fume extraction guns operate by capturing the fume generated by the welding process right at the source, over and around the weld pool. Various manufacturers have proprietary means of constructing guns to conduct this action, but at a basic level they all operate similarly: by mass flow, or the movement of material. This movement occurs by way of a vacuum chamber that suctions the fumes through the handle of the gun, into the gun’s hose through to a port on the filtration system (sometimes informally referred to as a vacuum box) like the Miller FILTAIR® 215 High-Vacuum Fume Extractor. The welding fumes that these guns remove are composed of a combination of the filler metal and base material. Some fume extraction guns feature adjustable extraction control regulators at the front of the gun handle, which allow welding operators to increase suction as needed (without affecting shielding gas coverage), while others provide this function internally. Regardless of the manner, the ability to balance between the downward flow of shielding gas and the upward flow of the suctioned air is critical. The fume extraction gun needs to provide the appropriate amount of shielding gas to protect the weld from defects such as porosity, without sacrificing the ability to suction fumes efficiently enough to protect the welding operator. The balance allows the weld pool time to react and solidify, and gives the fume particles time to decelerate so they are easier to extract. Typically, fume extraction guns are larger than regular welding guns and tend to be bulky due to the vacuum and hose necessary to extract the fumes. For that reason, some manufacturers create fume extraction guns with a vacuum hose swivel on the rear of the handle to make them easier to maneuver. Manufacturers have also, since fume extraction guns were first introduced (in the late 1960s and early 1970s), found ways to engineer internal components to minimize the handle weight in order to reduce operator fatigue. Fume extraction guns are well-suited for applications using solid welding wire and those in confined spaces. These include, but are not limited to applications in the shipbuilding and heavy equipment manufacturing industries, as well as general manufacturing and fabrication. They are also ideal for welding on stainless steel applications, as this material generates greater levels of hexavalent chromium, and on mild and carbon steel applications. The guns also work well on high amperage and high deposition rate applications and are available, typically, in 300 to 600 amp ranges. Fume extraction guns attach to a localized filtration system, as shown here. Fume removal occurs by way of a vacuum chamber in the fume extraction gun that suctions the fumes through the handle of the gun, into the gun’s hose through to a port on the filtration system. For the best results, fume extraction guns should be used for in-position welding, such as on flat butt welds. In this position, they can most effectively capture fume particles as they rise from the weld pool. In out-of-position welds, the energy of the fume particles causes them to rise at a high rate, making it more difficult for the fume extraction gun to draw them downward and through the vacuum hose. One distinct advantage to fume extraction guns is that they remove the fumes at the source. This will minimize the amount that enters the welding operator’s immediate breathing zone. As with any piece of welding equipment, fume extraction guns benefit from preventive maintenance. Caring for them is similar to caring for a standard GMAW gun. Regularly check for tight connections throughout the length of the fume extraction gun to ensure good electrical flow. Minimizing electrical resistance helps ensure consistent weld quality and prevent premature failure of the front-end consumables — contact tip, nozzle and diffuser. Frequently inspect the nozzle and contact tip for signs of spatter build-up, too, as such build-up can obstruct shielding gas flow and cause weld defects that ultimately will need to be reworked. Spatter build-up can also cause consumables to fail prematurely. Replace the consumables if spatter build-up appears or clean them according to the manufacturer’s recommendation. In some cases the shroud that surrounds the nozzle may also have to be replaced or cleaned free of spatter. To ensure optimal fume extraction capabilities, inspect the vacuum hose regularly for damage, including cuts or kinks that could lead to loss of suction. Replace a damaged vacuum hose as necessary and dispose of it according to the manufacturer’s and/or an industrial hygienist’s directions. Visually inspect the handle for cracks or missing screws, and also check that the gun’s trigger is not sticking or otherwise malfunctioning. Replace or repair these components as necessary. Finally, maintenance on the liner is also important. As with the vacuum hose, use compressed air to clear out any potential blockages during welding wire changeovers or when removing the wire from the gun. Spending an extra few minutes clearing out any debris from the liner can save considerably more time than troubleshooting the weld defects and equipment problems that can result from blockages. Also, track the amount of time that it takes for a liner to wear during the course of the welding operation. Replace the liner prior to that in the future to prevent downtime for replacement during shifts or problems with wire feeding or quality. When in doubt about maintenance or any other aspect of using a fume extraction gun, consider working with a trusted welding distributor, certified industrial hygienist and/or the fume extraction gun manufacturer to address any questions or concerns. Proper use of this equipment can help provide optimal results, and improve the safety and comfort of the welding environment. Our Bernard® BTB and TGX™ MIG Gun boxes are undergoing a packaging change with a fresh new look. While the exterior is changing, the MIG guns inside remain the same — delivering the trusted performance and reliability you depend on. Please be advised you may notice both old and new packaging during the rollout as this change will happen gradually. Effective February 19, 2025, Rear Load liners L3B-10 and L4B-10 are discontinued. Rear Load liners L3B-15 and L4B-15 directly replace L3B-10 and L4B-10, respectively. These replacements are 15ft (4.57 m) in length. For questions, please contact Customer Service by phone at 1.855.MIGWELD (644.9353) or email at cs@itwmig.com. We have expanded the nozzle options available in our AccuLock™ S and Tregaskiss® product families. For AccuLock™ S, we have added the following nozzle options: * For use with Miller Electric HD (High-Deposition) MIG CV GMAW process. For Tregaskiss®, we have added the following nozzle option: * For use with Miller Electric HD (High-Deposition) MIG CV GMAW process. If you have any questions, please call or email our Customer Service team at 855.MIGWELD (644.9353) or cs@itwmig.com. Regardless of your experience level, keeping your weld environment safe is a top priority. A multifaceted approach to fume mitigation can help you maximize safety and efficiency. Could it be time to take a closer look at your fume control strategies? Read our article published in the February issue of Fabricating & Metalworking. As part of our on-going simplification efforts, we are renaming our current selection of MIG gun liners. This change is effective now, as you will see our literature and website content being updated to reflect the simplified naming structure. We offer four different liner types between our semi-automatic and automation MIG guns. The chart below will show the previous liner name/reference as well as the updated liner name/reference. It’s important to note that the liners themselves are not changing. We will continue to deliver the same premium quality liners, using the same part numbers as we currently do. If you have any questions, please call or email our Customer Service team at 855.644.9353 (MIGWELD) or cs@itwmig.com. Due to low demand, effective February 7, 2025, Tregaskiss will discontinue TOUGH LOCK standard duty gas diffuser 404-25. TOUGH LOCK standard duty gas diffuser 404-10-25 directly replaces 404-25.This replacement is compatible with tapered, standard duty contact tips (403-2-XX, where XX represents wire size). Diffuser 404-10-25 includes a set screw, as shown in the image below. No adjustments will need to be made to the set screw before or after installation. Previously, 404-25 did not have a set screw. For questions, please contact Customer Service by phone at 1.855.MIGWELD (644.9353) or email at cs@itwmig.com. For the past 40 years, 4-Star Trailers in Oklahoma has built high-quality aluminum stock and horse trailers. Aluminum is lightweight, corrosion-resistant, and strong—ideal for trailers designed to endure tough road conditions. However, welding aluminum with a push-pull gun has its challenges. The heaviness of the tool can make it difficult to maneuver in tight angles, and the added weight can lead to welder fatigue, especially when working on large parts or frames. Additionally, this setup can cause delays in production timelines due to discomfort and inefficiency during long hours of use. Before switching to the Bernard® BTB Semi-Automatic Air-Cooled MIG Gun, the team regularly faced feeding issues. The feeding problems were especially noticeable when working on large aluminum parts, causing disruptions and affecting their ability to keep up with demanding production schedules. The difficulty in maneuvering the push-pull gun, coupled with the physical strain it placed on welders, contributed to frequent delays and a slower pace of work. The BTB Gun has been a game-changer. It pushes aluminum wire long distances with ease, something that wasn’t possible with the previous system. Its design is lightweight and maneuverable, making it far easier for welders to handle, especially in tight spots. This has significantly reduced fatigue, allowing the team to work longer and more comfortably without sacrificing quality. The customizable neck lengths of the BTB Gun are another huge advantage, allowing welders to reach into tight angles or handle bigger components with greater ease. The Easy Feed Liner in the BTB Gun reduces friction, making it simpler to feed aluminum wire and minimizing downtime—critical for maintaining a steady workflow in a busy shop. With fewer interruptions, the team is able to stick to production goals and meet deadlines more effectively. The use of AccuLock consumables also contributes to less maintenance, as they last longer than other options, cutting down on the frequency of replacements and the time spent on maintenance tasks. The biggest benefit? The team is more productive and satisfied with their work. With fewer interruptions and smoother operations, they’re able to produce high-quality welds faster. The BTB Gun has not only made their jobs easier but also helped the business run more efficiently. It’s become an indispensable tool in their shop, enabling them to build even tougher, more dependable trailers while improving overall productivity and welder satisfaction. Due to low demand, effective January 17, 2025, the following jacketed liners will be discontinued: There is no suggested replacement for these items. These jacketed liners were previously used in semi-automatic applications but are no longer compatible with our current MIG gun offerings. For questions, please contact Customer Service by phone at 1.855.MIGWELD (644.9353) or email at cs@itwmig.com. To continue to provide the best products and solutions to our customers, we routinely review, assess and evaluate our product line-up to ensure their features and benefits still hold their value. Accordingly, we have decided to discontinue our AutoLength™ power pins, effective January 10, 2025. These AutoLength pins are currently used across both semi-automatic and robotic/fixed automatic product lines. Until the effective date, you can still purchase existing configurations as well as replacement AutoLength pins (or until inventory is depleted, whichever occurs first). The charts below show the standard power pin that replaces each AutoLength option for both welding applications. You may also find instructions here for replacing an AutoLength power pin with a standard power pin. To configure a new MIG gun part number using a standard power pin, please utilize our online configurators. Your new configuration will also include a full parts list. If you have any questions or need assistance configuring a new gun or finding a replacement part number, please contact our Customer Service Team by phone at 1.855.MIGWELD (1.855.644.9353) or via email at CS@itwmig.com. Effective October 11, 2024, the following 100-pack diffusers will be packaged in boxes instead of bags. The box dimensions are 6” x 6” x 4” (15.24cm x 15.24cm x 10.16cm). Due to low demand, effective December 13, 2024, the following QUICK LOAD liners will be discontinued: As a suggested replacement, we offer conventional liners (rear loading). These liners are currently used across both semi-automatic and robotic/fixed automatic product lines. On the effective date, these seven QUICK LOAD liners will no longer be available, removed from our product configurators, and guns previously configured with these liners will no longer be available for purchase. DISCONTINUED PRODUCT | Elliptical Diffusers
DISCONTINUED PRODUCT | Elliptical Conversion Diffusers
Part Number 4235T 4335T 4435T 4635T 4635T-116 PRODUCT UPDATE — Configurator Simplification, BTB Semi-Automatic MIG Gun
PRODUCT UPDATE – Configurator Simplification,
BTB Semi-Automatic MIG Gun
4 Reasons Genuine Consumables Lead to Better MIG Welds
4 Reasons Genuine Consumables Lead to Better MIG Welds
3. Using low-quality products limits your manufacturer’s ability to helpThe New Clean Air E™ Fume Extraction MIG Gun Offers Superior Fume Capture, Enhanced Ergonomics
The New Clean Air E™ Fume Extraction MIG Gun Offers Superior Fume Capture, Enhanced Ergonomics
Up to 95% fume capture efficiency and optimized design make workspaces safer and reduce welder strain
Product Guide: Clean Air E™ – Changing the Y Connector
Product Guide: Clean Air E™ – Changing the Y Connector
Product Guide: Clean Air E™ – Connecting to a Fume Extraction Unit
Product Guide: Clean Air E™ – Connecting to a Fume Extraction Unit
Product Guide: Clean Air E™ – Replacing the Neck and Trigger
Product Guide: Clean Air E™ – Replacing the Neck and Trigger
Product Guide: Clean Air E™ – Changing Shrouds to Maximize Fume Extraction
Product Guide: Clean Air E™ – Changing Shrouds to Maximize Fume Extraction
Product Guide: Clean Air E™ – Changing Out the Hose
Product Guide: Clean Air E™ – Changing Out the Hose
Attacking Weld Fume at the Source
Attacking Weld Fume at the Source
The basics
Benefits of the Bernard® Clean Air™ E Fume Extraction Gun
Maximizing Performance
Proper maintenance and consumable usage
Fume extraction guns can provide results
Learn more about the Bernard® Clean Air E™
Fume Extraction Guns: Understanding the Basics
Fume Extraction Guns: Understanding the Basics
The basics of fume extraction guns
Applications, advantages and limitations
Maintenance tips
PACKAGING UPDATE — New Bernard® BTB and TGX™ MIG Gun Boxes
PACKAGING UPDATE — New Bernard® BTB and TGX™ MIG Gun Boxes
Discontinued Liners: L3B-10, L4B-10
Discontinued Liners: L3B-10, L4B-10
NEW PRODUCT — Expanded AccuLock™ S and Tregaskiss® Nozzle Offering
NEW PRODUCT — Expanded AccuLock™ S and Tregaskiss® Nozzle Offering
Part Number Bore Size Tip Position Material Quantity Compatibility N-A1218C 1/2″ 1/8’’ recess Copper 10 AccuLock™ S – Large N-A1214C 1/2″ 1/4’’ recess Copper 10 AccuLock™ S – Large N-A3412C* 3/4″ 1/2’’ Copper 10 AccuLock™ S – Large Part Number Bore Size Tip Position Material Quantity Compatibility 401-9-75* 3/4″ 1/2″ Copper 10 TOUGH LOCK® Diffuser
404-32 (Robotic)
404-26 (Semi-Automatic)
AccuLock™ R Diffuser
D-ATSH (Slip-On)The Importance of Implementing a Layered Approach to Fume Mitigation
The Importance of Implementing a Layered Approach to Fume Mitigation
Update to Liner Descriptions
Update to Liner Descriptions
Previous Liner Name/Reference Updated Liner Name/Reference AccuLock S (Dual Lock) Liner Front Load Liner Conventional Liner Rear Load Liner QUICK LOAD® Pro Liner (Automation Only) E-Z Feed™ Liner QUICK LOAD® (There is no name change for this product) Discontinued: TOUCH LOCK® standard duty gas diffuser, Part Number 404-25
Discontinued: TOUCH LOCK® standard duty gas diffuser, Part Number 404-25
Bernard® BTB Gun Transforms Aluminum Welding for 4-Star Trailers
Bernard® BTB Gun Transforms Aluminum Welding for 4-Star Trailers
Discontinued Parts: Jacketed Liners, LJ-XXXX-XX
Discontinued Parts: Jacketed Liners, LJ-XXXX-XX
Part Number Description LJ-3545-15 Jacketed liner, 0.035″ – 0.045″, 15′ LJ-3545-25 Jacketed liner, 0.035″ – 0.045″, 25′ LJ-5262-12 Jacketed liner, 0.052″ – 1/16″, 12′ LJ-5262-15 Jacketed liner, 0.052″ – 1/16″, 15′ LJ-5262-25 Jacketed liner, 0.052″ – 1/16″, 25′ Discontinued Products – AutoLength™ Power Pins
Discontinued Products – AutoLength™ Power Pins
PACKAGING CHANGE — Diffusers 404-XX, D-ATSH-100, D-ATTH-100
PACKAGING CHANGE — Diffusers 404-XX,
D-ATSH-100, D-ATTH-100100-pack Diffusers Description 404-18 TOUGH LOCK®, Standard Duty 404-20 TOUGH LOCK, HD 404-26 TOUGH LOCK, HD 404-30 TOUGH LOCK, HD 404-31 TOUGH LOCK, HD 404-32 TOUGH LOCK, HD for Robotic D-ATSH-100 AccuLock™ R Diffuser, Slip-On D-ATTH-100 AccuLock R Diffuser, Thread-On Discontinued Parts: QUICK LOAD® Liners, 415-30-XXQ, 415-564-XXQ, 415-332-XXQ
Discontinued Parts: QUICK LOAD® Liners, 415-30-XXQ, 415-564-XXQ, 415-332-XXQ
QUICK LOAD® Liner Tregaskiss® Conventional Liner
(Robotic/Automation)Bernard® Conventional Liner
(Semi-Auto)415-30-6Q 415-30-25 L2A-15 415-30-15Q 415-30-25 L2A-15 415-564-6Q 415-564-6 L6A-15 415-564-15Q 415-564-15 L6A-15 415-564-25Q 415-564-25 L6A-25 415-332-15Q 415-332-15 L7A-15 415-332-25Q 415-332-25 L7A-25
Please use our online configurators and/or consult Customer Service to find a suitable replacement by phone at 1.855.MIGWELD (644.9353) or email at cs@itwmig.com.